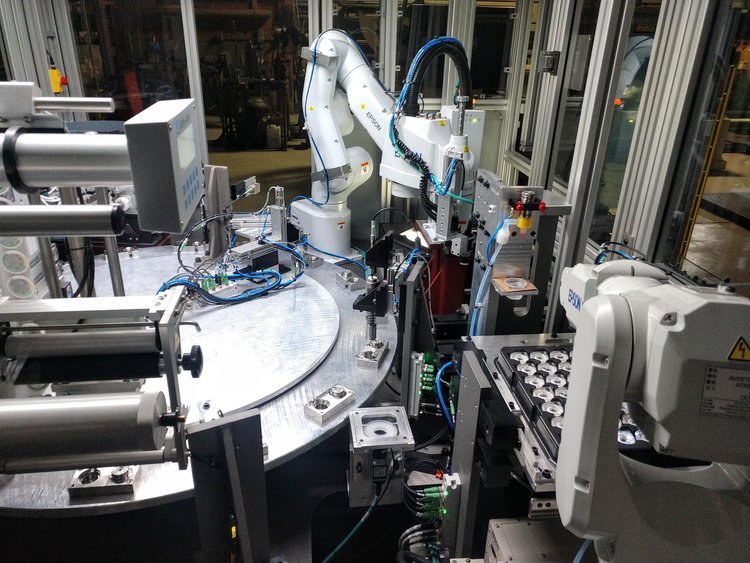
Indexing, Assembly and Testing Machines
Our indexing assembly machines are tailor-made to the product and particularities of the assembly and process being implemented. A machine can be dedicated to the manufacture of a single product or products with multiple variants. Thanks to modularity of stations, interchangeability of tooling, flexibility of power supplies, and integration of robots, machines can be efficiently changed over between product styles.
Before designing a machine, FRANKLIN AUTOMATION performs de-risking (Proof of Principle) of critical operations in order to simulate assembly processes as well as feeding orientation and behavior of difficult components. After the de-risking phase, proven concepts are then integrated into final assembly machine designs.
Strengths of Indexed Machines Include:
Robustness, reliability, and repeatability provide guaranties of high performance
Accessibility, compactness, and process visibility facilitates convenient machine operation and maintenance
Readily available technologies for making complex assemblies
Low maintenance cost and ease of service without change of settings
Connectivity, interface providing remote diagnosis capabilities
Our Machines
Automatic Indexing Machines by FRANKLIN AUTOMATION
FRANKLIN supplies indexing machines with outputs ranging from 800 to 3,600 cycles per hour. Actual production rates can be increased by assembling more than one component per machine cycle. For this reason, it is possible for FRANKLIN to provide assembly and testing machines with production rates as high as 7,200 parts per hour. FRANKLIN machines are primarily designed and built through the integration of exiting automation technologies including extensive quality control systems such as vision inspection, LVDT measurement, Leak and Pressure test systems and more; Furthermore, for fully automated systems, FRANKLIN commonly integrates vibratory feeder bowls, vision guided robots, and tray unloading systems for automatically feeding parts to their assembly machines. All machines are equipped with a highly developed machine control system including an AB PLC and HMI (unless otherwise specified); pneumatic systems are designed with Festo or SMC valve banks and both electricals and pneumatics are mounted in enclosures.
Automatic Indexing Machines by SOCIETE GUY NEYRET (GNSA)
GNSA specializes in the supply of indexing machines running from 2,400 to 14,400 parts per hour with annual production volumes ranging from 10 – 100M pieces per year. Operations are carried using either rotary indexing rings or magnetic linear conveyors. With either chassis, GNSA designs and integrates modular mechanical and electrical cam manipulators (eManip). It is common for the eManip systems to integrate several functions at one assembly station thereby making it possible to significantly reduce the machine footprint. On line quality control systems include any brand of vision system, sensors, and complex test systems. Automatic parts feeding is performed by vibratory feeder bowls, palletizers, and/or flexible feeding with vision guided robots.
Semi-automatic Assembly Machines by FRANKLIN AUTOMATION
Includes machines with assembly rates of 500 – 700 pieces per hour up to 5M per year. These machines are ideal for small and medium series production including manual parts loading stations which can be combined together with automated feeding stations for more difficult parts. These machines have all the same options and possibilities as with the automated versions described above including on line quality control and service as well as interchangeable tooling or robots with removable EOAT for producing numerous product variants.
Manual Assembly Station by FRANKLIN AUTOMATION
Includes 1 to 4 assembling and testing stations in which an operator is required to position the components on their fixtures; once loaded and/or transferred from fixture to fixture, the machine can perform its assembly and testing functions on the products. These types of assembly stations are ideal for lower volume production requiring one or more assembly operations together with on line quality control. These machines commonly include interchangeable fixture nests for producing a variety of assemblies and a high level of built-in poka-yoke features to ensure quality and efficiency of change overs.